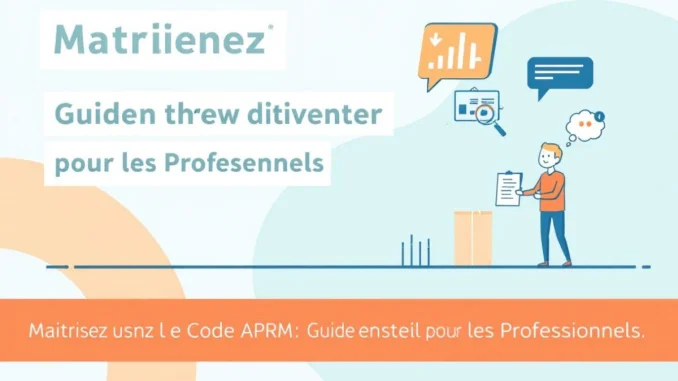
Le code APRM (Analyse et Prévention des Risques Mécaniques) constitue un outil fondamental pour les professionnels de la sécurité industrielle. Ce système de codification normalisé permet d’identifier et d’évaluer les risques liés aux équipements mécaniques. Sa maîtrise s’avère indispensable pour optimiser la sécurité des travailleurs et la conformité réglementaire des installations. Ce guide approfondi vous permettra d’acquérir une compréhension complète du code APRM et de son application pratique dans divers contextes industriels.
Fondements et principes du code APRM
Le code APRM repose sur une approche systématique d’identification et d’évaluation des risques mécaniques. Il s’articule autour de plusieurs principes fondamentaux qui guident son utilisation :
- Analyse exhaustive des dangers potentiels
- Évaluation objective de la probabilité et de la gravité des risques
- Hiérarchisation des mesures de prévention
- Documentation rigoureuse des analyses et des décisions
La méthodologie APRM s’appuie sur une grille d’analyse standardisée qui permet de décomposer chaque équipement en ses éléments constitutifs. Pour chaque composant, les risques potentiels sont identifiés et cotés selon des critères prédéfinis. Cette approche structurée facilite une évaluation complète et cohérente des risques mécaniques sur l’ensemble d’une installation industrielle.
L’un des avantages majeurs du code APRM réside dans sa flexibilité d’application. Il peut être adapté à une grande variété de secteurs industriels, depuis l’industrie manufacturière jusqu’aux installations pétrolières en passant par l’agroalimentaire. Cette polyvalence en fait un outil précieux pour les professionnels de la sécurité intervenant dans des environnements diversifiés.
La mise en œuvre efficace du code APRM nécessite une formation approfondie des équipes chargées de son application. Les analystes doivent maîtriser non seulement la méthodologie elle-même, mais aussi posséder une solide connaissance des processus industriels et des technologies mécaniques concernées. Cette expertise combinée permet d’obtenir des résultats d’analyse pertinents et exploitables.
Méthodologie d’application du code APRM
L’application pratique du code APRM suit une méthodologie structurée en plusieurs étapes clés :
- Définition du périmètre d’analyse : Cette phase initiale consiste à délimiter précisément le champ d’application de l’étude APRM. Il peut s’agir d’un équipement spécifique, d’une ligne de production complète ou même d’une usine entière.
- Collecte des données techniques : L’analyste rassemble toutes les informations pertinentes sur les équipements concernés : plans, schémas, manuels techniques, historique de maintenance, etc.
- Décomposition fonctionnelle : Chaque équipement est décomposé en ses éléments constitutifs (sous-systèmes, composants) pour permettre une analyse détaillée.
- Identification des dangers : Pour chaque élément, l’analyste répertorie les dangers potentiels en s’appuyant sur une liste standardisée de risques mécaniques (écrasement, cisaillement, coupure, etc.).
- Évaluation des risques : Chaque danger identifié est évalué en termes de probabilité d’occurrence et de gravité potentielle des conséquences. Cette évaluation s’appuie sur des grilles de cotation normalisées.
- Détermination des mesures de prévention : En fonction du niveau de risque évalué, des mesures de prévention appropriées sont définies selon une hiérarchie d’efficacité (élimination du danger, protection collective, protection individuelle, etc.).
- Documentation et reporting : L’ensemble de l’analyse est consigné dans un rapport structuré, incluant les résultats détaillés et les recommandations.
La rigueur méthodologique est essentielle tout au long du processus d’application du code APRM. Elle garantit l’exhaustivité de l’analyse et la fiabilité des résultats obtenus. Les professionnels expérimentés développent souvent des outils spécifiques (logiciels, bases de données) pour faciliter la mise en œuvre systématique de cette méthodologie.
L’un des défis majeurs dans l’application du code APRM réside dans la gestion de la complexité des systèmes industriels modernes. Les interactions entre différents équipements et processus peuvent générer des risques difficiles à anticiper. Une approche systémique et une collaboration étroite avec les opérateurs et les ingénieurs de production sont souvent nécessaires pour appréhender pleinement ces enjeux.
Interprétation et exploitation des résultats APRM
L’analyse APRM génère une masse considérable de données qu’il convient d’interpréter et d’exploiter judicieusement. Cette phase est critique pour transformer les résultats bruts en actions concrètes d’amélioration de la sécurité.
La priorisation des risques constitue une étape clé de l’interprétation. Les risques identifiés sont généralement classés selon une matrice combinant probabilité et gravité. Cette hiérarchisation permet de concentrer les efforts et les ressources sur les dangers les plus critiques.
L’exploitation des résultats APRM doit s’inscrire dans une démarche d’amélioration continue de la sécurité. Les recommandations issues de l’analyse sont intégrées dans un plan d’action global, avec des responsabilités et des échéances clairement définies. Un suivi rigoureux de la mise en œuvre de ces actions est indispensable pour garantir l’efficacité de la démarche.
Les résultats de l’analyse APRM alimentent également la formation et la sensibilisation des opérateurs. Les risques identifiés et les mesures de prévention associées sont intégrés dans les procédures de travail et les programmes de formation à la sécurité. Cette diffusion des connaissances contribue à développer une véritable culture de la prévention au sein de l’organisation.
L’exploitation optimale des résultats APRM nécessite souvent une approche multidisciplinaire. La collaboration entre les experts en sécurité, les ingénieurs de conception, les responsables de maintenance et les opérateurs permet d’élaborer des solutions pragmatiques et efficaces pour réduire les risques identifiés.
Enfin, il est fondamental de considérer les résultats APRM comme un outil d’aide à la décision plutôt qu’une fin en soi. L’analyse fournit des informations précieuses, mais c’est aux responsables de l’entreprise qu’il incombe de prendre les décisions finales en matière de gestion des risques, en tenant compte des contraintes opérationnelles et économiques.
Intégration du code APRM dans la gestion globale de la sécurité
Le code APRM ne doit pas être considéré comme un outil isolé, mais comme une composante intégrée d’un système global de gestion de la sécurité. Cette intégration permet d’optimiser son efficacité et sa contribution à la prévention des risques industriels.
L’articulation entre l’APRM et les autres méthodes d’analyse de risques (HAZOP, AMDEC, arbre des causes, etc.) est particulièrement importante. Chaque méthode apporte un éclairage complémentaire sur les risques potentiels. Une approche coordonnée permet d’obtenir une vision exhaustive de la sécurité d’une installation.
L’intégration de l’APRM dans le processus de conception des équipements et des installations représente un enjeu majeur. L’application précoce de la méthodologie permet d’identifier et de traiter les risques dès les phases initiales du projet, réduisant ainsi les coûts et les difficultés liés à des modifications tardives.
La maintenance préventive constitue un autre domaine où l’intégration de l’APRM s’avère particulièrement pertinente. Les résultats de l’analyse alimentent directement les plans de maintenance, permettant de cibler les interventions sur les points critiques identifiés.
L’APRM joue également un rôle central dans la gestion du changement. Toute modification significative d’un équipement ou d’un processus doit faire l’objet d’une nouvelle analyse APRM pour évaluer son impact sur la sécurité globale de l’installation.
Enfin, l’intégration de l’APRM dans les systèmes de management de la sécurité certifiés (ISO 45001, par exemple) renforce la cohérence et l’efficacité de la démarche globale de prévention des risques professionnels.
Perspectives et évolutions du code APRM
Le code APRM, bien qu’éprouvé, continue d’évoluer pour répondre aux défis émergents en matière de sécurité industrielle. Plusieurs tendances se dessinent quant à son développement futur :
L’intégration des technologies numériques ouvre de nouvelles perspectives pour l’application du code APRM. Les outils de réalité virtuelle et augmentée permettent par exemple de simuler des situations à risque et d’évaluer l’efficacité des mesures de prévention de manière plus immersive et réaliste.
L’intelligence artificielle commence à être explorée pour automatiser certaines phases de l’analyse APRM, notamment l’identification des dangers potentiels à partir de bases de données historiques. Ces approches pourraient accélérer le processus d’analyse tout en améliorant sa précision.
La prise en compte croissante des facteurs humains et organisationnels dans l’analyse des risques constitue une autre tendance majeure. Les futures évolutions du code APRM devraient intégrer davantage ces aspects, reconnaissant leur rôle crucial dans la genèse des accidents industriels.
L’harmonisation internationale des pratiques APRM représente un enjeu important pour les entreprises opérant à l’échelle mondiale. Des efforts sont en cours pour développer des standards communs, facilitant la comparaison et l’échange d’informations entre différents pays.
Enfin, l’adaptation du code APRM aux nouvelles technologies industrielles (industrie 4.0, robotique collaborative, etc.) constitue un défi majeur. La méthodologie devra évoluer pour prendre en compte les risques spécifiques liés à ces innovations, tout en préservant sa robustesse et sa fiabilité.
En définitive, la maîtrise du code APRM s’impose comme une compétence incontournable pour les professionnels de la sécurité industrielle. Son application rigoureuse, combinée à une intégration judicieuse dans la stratégie globale de gestion des risques, permet d’optimiser la sécurité des installations tout en contribuant à l’amélioration continue des performances industrielles.